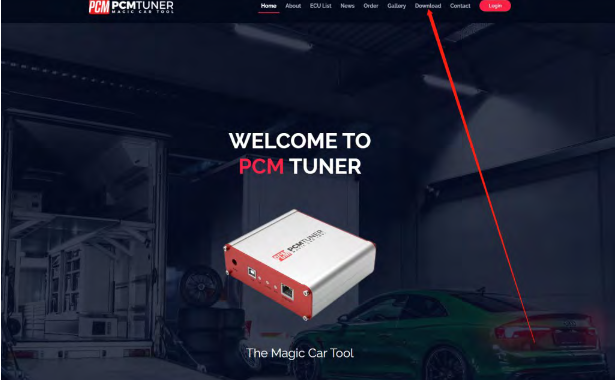
PCMtuner ECU Chip Tuning Tool Installation Guide
Preparation before installation: 1 Connect the device to the computer with power cable and USB cable, and plug the smart lock dongle into computer, like […]
Preparation before installation: 1 Connect the device to the computer with power cable and USB cable, and plug the smart lock dongle into computer, like […]
MPM ECU Chip Tuning Tool is the best American car ECU tuning tool. MPM has all GM protocols, OBD reads ECM and TCM. No token, no […]
MPM ECU TCU Chip Tuning Tool with VCM Suite from PCMTuner Team applicable for American Car ECUs All in OBD VCM Editor: SCAN, LOG, DIAGNOSE. […]
Both PcmTuner and ECUHelp ECU Bench Tool are new released ECU Programmer in 2022, Which one is better? Here is comparison table to help you […]
Can CG FC200 calculate the checksum like KTAG? Does it support virtual reading? Recently, many customers asked whether the CG FC200 supports the checksum function. Yes, […]
Recently a customer encountered some problems using iprog+ pro clone: when the firewall and windows defender were turned off, I have to wait many seconds […]
I have an xprog 6.12 ecu programmer. I close the internet, firewall and all antivirus software on my computer and already install Adobe. When I […]
Does CG FC200 support checksums? Many customers often ask themselves this question before purchasing a device. In fact, Auto ECU Programmer FC200 has its own data validation […]
Problem After installing the KESS V2 Software there are no connection diagrams regardless of the selected vehicle model or ECU. It just gives me a blank […]
Problem: Hi team, may you please assist. Under which ECU type must I read this with Yanhua Mini ACDP. I need to read Isn from […]
iProg clone programmer latest software V87 has been tested and verified working with no issue by obd2tool.com engineer. Version doesn’t matter, scripts are important. V87 […]
Yanhua Mini ACDP BMW + Module 11 can support to refresh BMW F series 6HP EGS on bench without soldering, this is a guide to show […]
CG FC200 ecu programmer is new device which is designed for ECU/EGS clone, a new ECU expert manufactured by CGDI company. Supports functions including data […]
Here share a real customer test report about using KESS V2 Ksuite 2.23 fw V5.017 to read and write ECU data on a 2009 Mercedes- Benz […]
If an ECU has been flashed with a defective software and other ECUs reports that it is missing,you need to recover it.So herewww.obd2tool.com show you […]
Copyright © 2025 | WordPress Theme by MH Themes